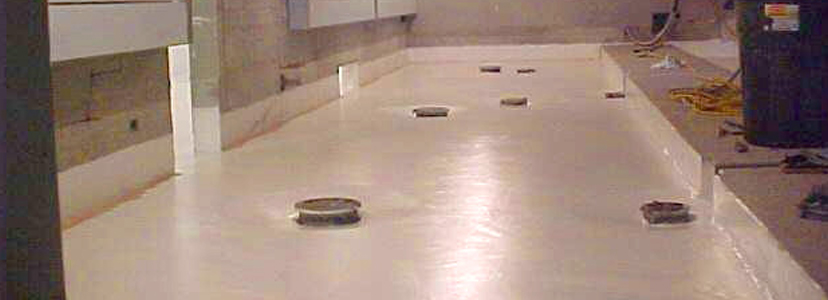
Boston’s Logan International Airport has undertaken a decade-long effort to bring the 82-year-old facility into the 21st century. One of the most significant improvements is the construction of Terminal A, the first entirely new terminal to be built since 1974 and the second largest. While adding 25 aircraft boarding positions, the terminal will also offer more than two-dozen concession and retail outlets to enhance the traveling experience. Being Logan Airport’s first truly sustainable or “green” structure, materials used during construction were required to have very low or no volatile organic compounds to maintain the indoor air quality. The fast-track schedule also put rigid time constraints on construction processes.
The restaurants being featured in Terminal A needed a waterproofing system under their floors that could withstand the caustic bleaches and chemicals used during cleaning that seep through grout and tile. To ensure ultimate protection, the waterproofing systems at Logan Airport were required to be 50+ mils. Standard systems used required three coats with two days between each and seven days after the third coat for a total of two weeks, which the schedule did not allow.
Tremco’s Vulkem 360NF/351NF Pedestrian Deck Coating System forms a seamless elastomeric membrane system that is waterproof, easy-to-clean and resistant to caustic cleaning chemicals. Specially formulated for odor-sensitive applications, water-cured Vulkem 360NF Polyurethane Basecoat can be applied to any thickness desired.
For restaurants in Terminal A contracting with Shawmut, two coats were applied for a total of 40 mils, allowing only one night between coats. Vulkem 351NF Polyurethane Topcoat was then applied with sufficient aggregate to form a final 15 mils and excellent bond for the mud-based tile bed. Water testing was done on the third day. Instead of 14 days, the entire process took three. Topped with pitched mud and quarry tile finish floors, the system was impenetrable.